Introduction: Understanding the Equipment of the Textile Industry
The textile industry is a vibrant tapestry of processes that transform raw fibers into the dazzling array of fabrics we see around us. Central to this transformation is the dyeing and finishing process. Dyeing, as the name suggests, imparts color to textiles, breathing life into plain fibers. The finishing process then enhances these dyed fabrics, giving them the desired texture, appearance, and wear-resistance, whether it’s the soft touch of a cashmere sweater or the glossy sheen of silk.
But achieving the perfect hue or the ideal texture isn’t just about applying the right dye or finish; it’s about doing so consistently, evenly, and efficiently. This is where the significance of reliable systems and infrastructure becomes paramount. Just as an artist relies on premium brushes to create masterpieces, the textile industry needs state-of-the-art process piping systems to ensure that dyes and finishes are applied impeccably. These systems become the silent, yet crucial, partners in delivering textiles that meet and exceed quality expectations, setting the stage for all the subsequent wonders that the world of fashion and design bring to our lives.
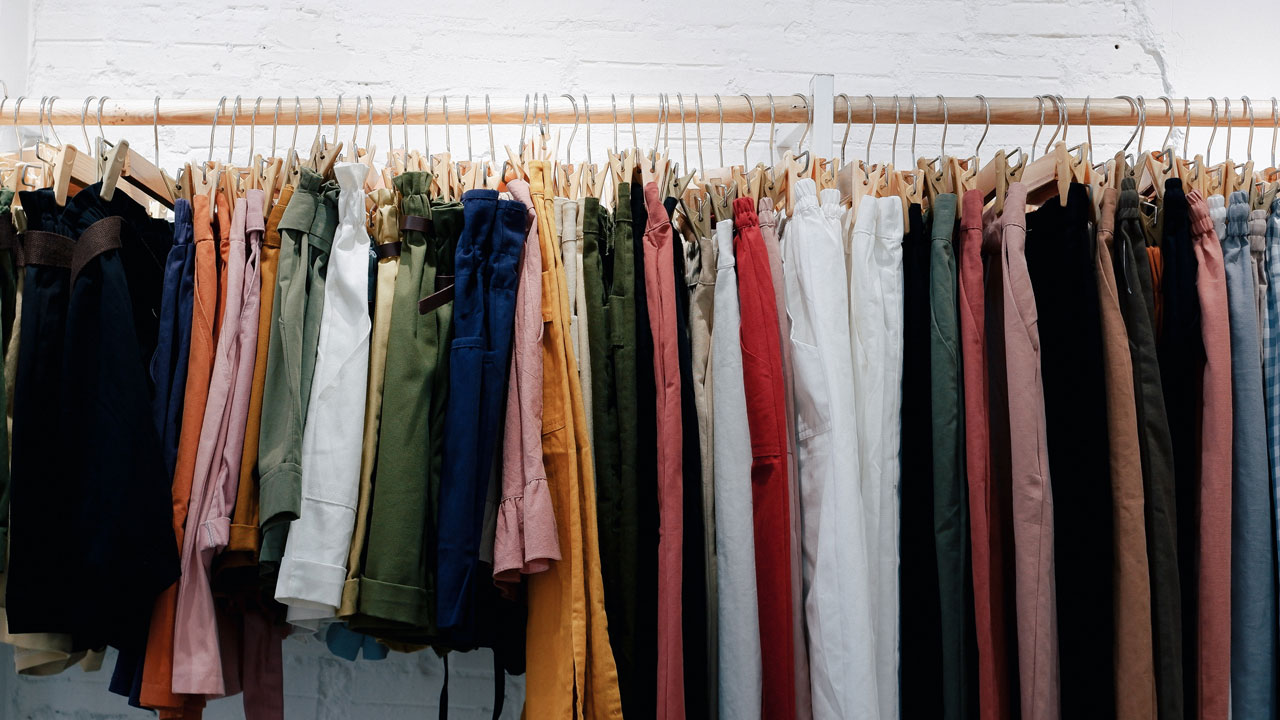
What is Process Piping?
Process piping is an intricate system designed to transport a variety of fluids, gases, chemicals, and other materials within industrial processes. These systems are tailored to meet the unique demands of specific industries and applications, ensuring the safe and efficient movement of substances necessary for a production process.
While both process piping and standard plumbing involve the transportation of fluids, their applications and designs are distinctly different:
1. Purpose: Standard plumbing systems are designed primarily for the transport and distribution of water, waste, and gas in residential, commercial, and public facilities. In contrast, process piping systems are tailored for industrial applications, catering to the specific needs of processes like chemical reactions, product manufacturing, and other specialized operations.
2. Materials Transported: Plumbing typically deals with potable water, sewage, and, in some cases, gas. Process piping, on the other hand, can carry a diverse range of substances, from corrosive chemicals in a chemical plant to dyes and finishes in a textile factory.
3. Design & Standards: Plumbing systems generally follow universal codes and standards, ensuring basic safety and functionality. Process piping systems, however, are designed with more intricate specifications, taking into account factors such as temperature, pressure, flow rate, and the nature of materials being transported. They adhere to industry-specific standards and regulations.
4. Complexity: While plumbing systems can be complex, especially in large buildings, process piping systems often involve a higher degree of complexity, integrating multiple inputs and outputs, varying pressure zones, and sophisticated control mechanisms.
In essence, while both process piping and plumbing revolve around transporting fluids, the specificities of their design, purpose, and the materials they handle set them apart, with process piping playing a pivotal role in the world of industrial manufacturing and production.
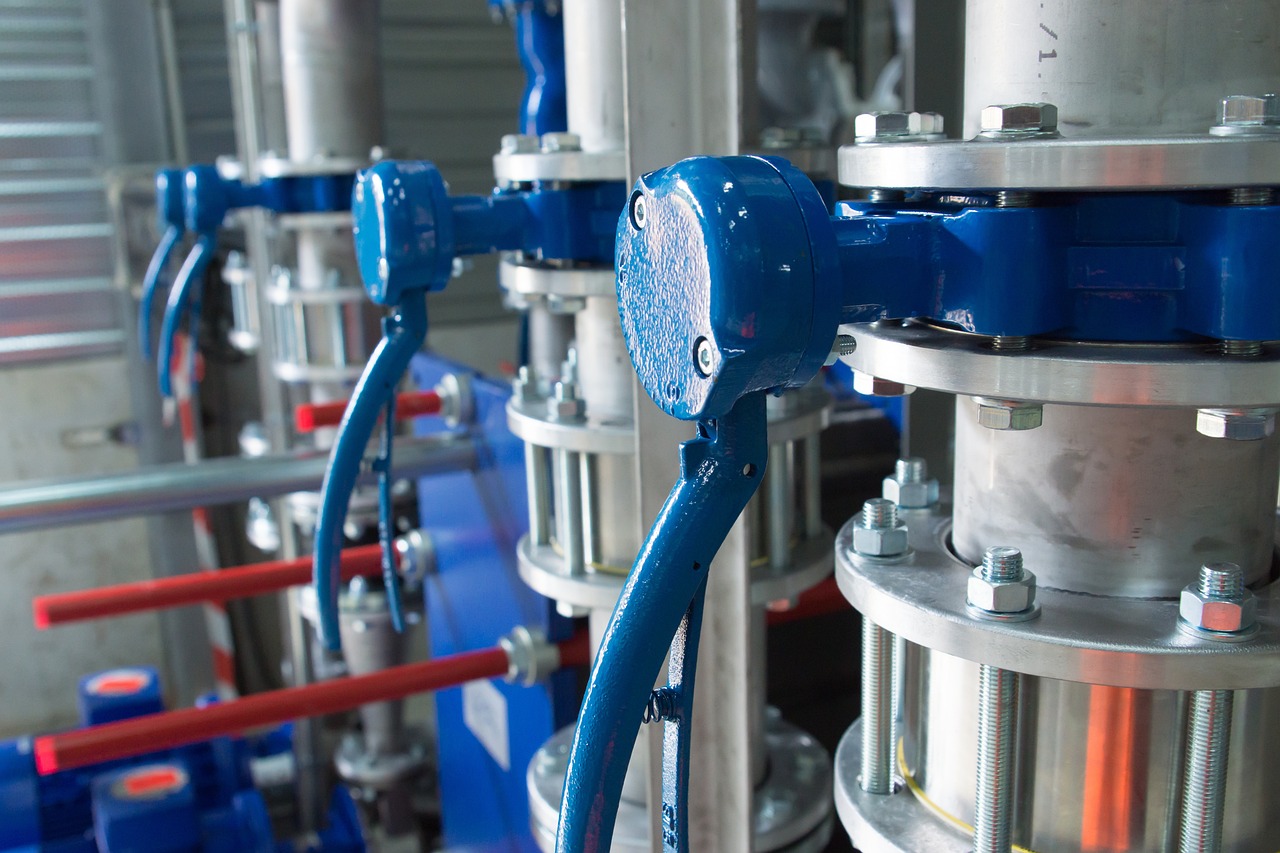
The Significance of Process Piping in Textile Manufacturing
The textile industry, with its myriad processes, ranging from the initial spinning of fibers to the final production of intricately designed fabrics, is a symphony of complex operations. At the heart of this symphony, ensuring harmony and consistency, is the process piping system.
Integration with Textile Production Stages:
1. Pre-Treatment: Before textiles can be dyed, they undergo a series of pre-treatment processes like scouring, bleaching, and mercerizing. Process piping systems efficiently transport various chemicals and water required for these stages, ensuring textiles are prepared uniformly.
2. Dyeing and Printing: The core coloring processes, whether dyeing the fabric in vats or printing specific designs, demand precise control over the flow of dyes, chemicals, and water. Process piping ensures that these substances are delivered accurately, maintaining color consistency and quality.
3. Finishing: Post-dyeing, fabrics undergo various finishing processes to achieve desired qualities. Whether it’s softening, making the fabric wrinkle-resistant, or adding waterproofing agents, process piping systems play a role in transporting the necessary chemicals and treatments.
4. Waste Management: Once processes are complete, waste products need to be safely transported and treated. Efficient process piping aids in moving waste products to treatment facilities, ensuring environmental compliance.
Need for Specialized Piping Systems:
Textile manufacturing isn’t just about moving water and dyes. It’s about transporting a range of substances, each with its specific properties, through stages that might have varying temperature and pressure requirements.
1. Chemical Resistance: Many chemicals used in textile processing can be corrosive. Piping systems must be resistant to such chemicals to ensure durability and safety.
2. Temperature Control: Some stages, like heat setting in finishing or the actual dyeing process, require the fluids to be at specific temperatures. The piping systems must be able to maintain these temperatures throughout.
3. Flow Rate Regulation: The speed at which substances are transported can impact the final product’s quality. For instance, the rate at which dye is introduced can affect the fabric’s color uniformity. Specialized piping systems can regulate flow rates as needed.
4. Safety: With the numerous chemicals involved, there’s always a risk of reactions if substances mix inadvertently. Specialized piping systems ensure that such cross-contaminations don’t occur.
Process piping isn’t just a transport mechanism in textile manufacturing; it’s a critical tool that directly influences product quality, efficiency, and safety. With the industry’s intricate requirements, there’s an undeniable need for specialized piping systems, tailor-made to cater to textile processes’ unique demands.
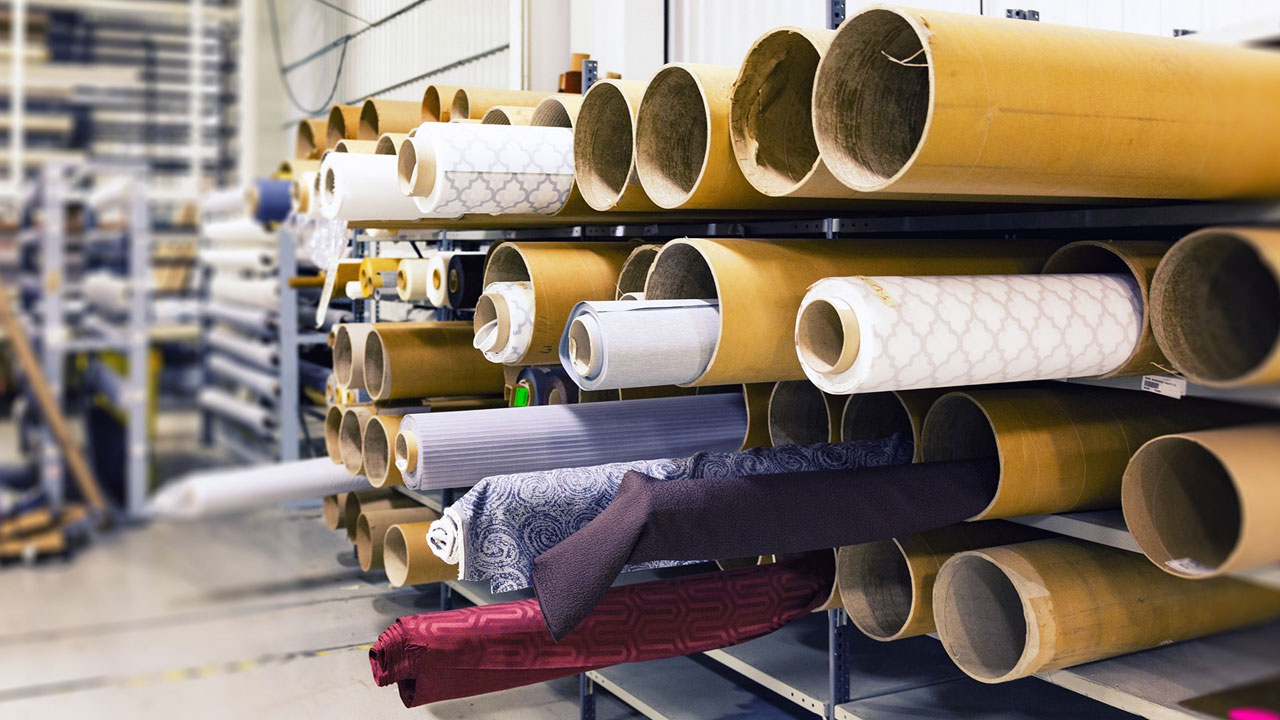
Role in Finishing
Finishing, often considered the final touch in textile production, imparts desired qualities to fabrics, making them ready for the consumer. From the silky feel of a scarf to the wrinkle-resistant shirt, finishing processes play a crucial role. Integral to these processes are the intricate process piping systems, ensuring that finishing agents and treatments are delivered optimally.
Chemical Finishing:
Chemical finishing bestows textiles with a plethora of functional and aesthetic properties:
1. Delivering Finishing Agents: Piping systems transport a multitude of chemical agents to the finishing baths or machines. These chemicals, ranging from softeners to flame retardants, are delivered in precise quantities, ensuring consistency across the textile batch.
2. Versatility: Different textiles require different finishes. The adaptability of process piping systems allows for the introduction of a varied array of finishing chemicals, from water-repellents for outdoor gear to antimicrobial finishes for healthcare textiles.
3. Consistency & Quality: To ensure that every inch of the fabric gets uniformly treated, process piping ensures a steady, even flow of finishing solutions. This uniformity is key to producing high-quality finished textiles.
Mechanical Finishing:
While mechanical finishing primarily involves physical processes, process piping still plays a pivotal role:
1. Calendaring: In this process, fabrics are passed between heated rollers to achieve a smooth, glossy surface. Process piping systems supply steam or other heating agents to these rollers, maintaining the desired temperature for optimal finishing.
2. Raising: To provide a fuzzy or napped surface to textiles, fabrics are passed over rollers with protruding wire ends. The lubricants or solutions needed to facilitate this process and protect the fabric are delivered effectively via process piping.
Environmental Considerations:
With increasing awareness of environmental sustainability, the textile industry faces challenges in waste management and resource conservation:
1. Waste Management: Post-finishing, there’s often residual chemical runoff. Process piping systems, designed with environmental considerations, channel these residues to treatment facilities, ensuring harmful chemicals don’t enter the ecosystem.
2. Water Conservation: With advanced piping systems, it’s possible to recycle and reuse water in many stages of the finishing process. Such systems ensure minimal water wastage, playing a part in conserving this precious resource.
3. Reducing Chemical Wastage: Efficient piping systems ensure that chemicals are delivered in precise amounts, reducing excess use. Additionally, systems can be designed to recycle and reuse certain chemicals, further reducing wastage.
In the grand tapestry of textile production, the finishing process stands as the final brushstroke, transforming raw fabrics into masterpieces. At every step, process piping systems support, enhancing efficiency, ensuring quality, and upholding environmental responsibilities. Their role, often behind the scenes, is pivotal in shaping the textile products we use and love every day.
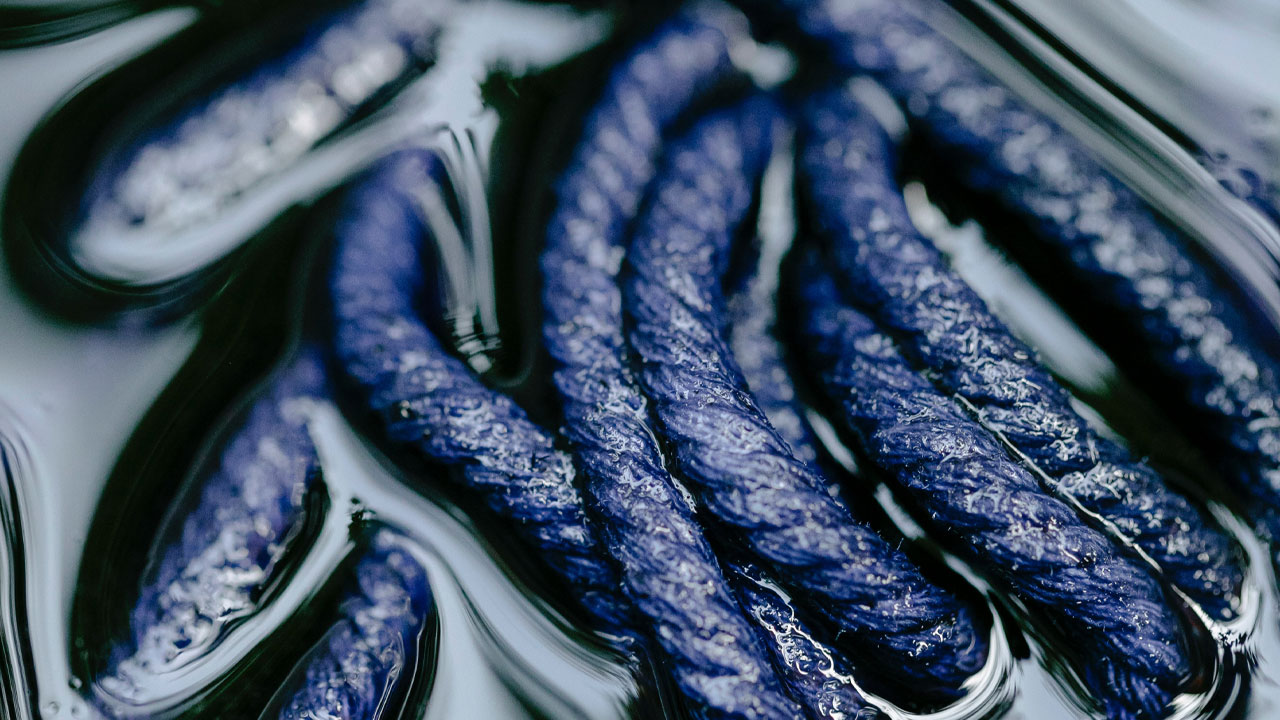
Benefits of Efficient Process Piping in Textile Dyeing and Finishing
The dyeing and finishing stages of textile production, where raw fabrics transform into vibrant and user-ready materials, demand precision and quality. Efficient process piping systems play a critical role in ensuring these demands are met. Let’s delve into the manifold benefits of effective process piping in this realm:
Consistency: Achieving Uniform Results
1. Precision in Delivery: A top-notch process piping system guarantees that dyes, chemicals, and finishing agents are delivered uniformly across the fabric. This ensures that colors are consistent, and finishes are evenly applied, resulting in a product that meets high standards of quality.
2. Temperature and Pressure Control: Consistency in dyeing and finishing also hinges on maintaining the right temperature and pressure. Efficient piping systems come equipped with mechanisms to regulate both, ensuring optimal conditions for every phase.
Efficiency: Speeding up Production and Reducing Wastage
1. Streamlined Flow: Properly designed piping systems facilitate a smooth and uninterrupted flow of materials. This aids in speeding up production processes, reducing the time taken from raw fabric to finished product.
2. Reduction in Overuse: With precision delivery, there’s a significant reduction in the overuse of dyes and chemicals. This not only cuts costs but also minimizes wastage.
Safety: Ensuring Safe Handling and Transportation
1. Chemical Resistant Materials: Given the array of chemicals used in dyeing and finishing, it’s essential for piping systems to be made of materials resistant to corrosion and chemical reactions. This ensures the safe transport of chemicals without the risk of leaks or ruptures.
2. Temperature Management: Efficient process piping systems are designed to handle and maintain hot liquids, ensuring they are safely transported without causing harm or posing a risk to workers.
Sustainability: Playing a Role in Conservation and Reduction
1. Water Reuse: Advanced piping systems can be designed to recycle and reuse water, significantly reducing the consumption of this precious resource.
2. Waste Treatment: With the focus on sustainability, modern process piping systems often integrate with waste treatment facilities, ensuring that chemical residues are treated and neutralized before being released.
3. Energy Conservation: Efficient process piping systems, especially those with integrated temperature control, can lead to energy savings, reducing the overall carbon footprint of the dyeing and finishing process.
The benefits of efficient process piping in textile dyeing and finishing extend far beyond just functional advantages. They touch upon the core values of quality, safety, efficiency, and sustainability, making them indispensable in producing textiles that resonate with modern consumer and environmental expectations.
Challenges and Solutions in Process Piping for Textile Dyeing and Finishing
Process piping, despite its pivotal role in textile dyeing and finishing, comes with its set of challenges. Addressing these effectively is crucial to ensure both product quality and operational efficiency. Let’s explore some of the primary challenges and the solutions to counteract them:
1. Corrosion from Chemicals
Challenge: Many chemicals used in dyeing and finishing are corrosive. Regular exposure can degrade piping materials, leading to leaks, ruptures, and system failures.
Solution: Utilizing corrosion-resistant materials such as stainless steel, or applying protective coatings inside pipes can significantly increase their lifespan. Additionally, regular maintenance checks and timely replacement of worn-out sections ensure the system remains robust.
2. Temperature Management
Challenge: The dyeing and finishing processes often require fluids to be at specific temperatures. Maintaining these temperatures, especially in large-scale operations, can be challenging.
Solution: Incorporating advanced temperature control mechanisms within the piping system, such as integrated heat exchangers and insulating materials, can ensure that fluids remain at desired temperatures. Regularly calibrating and checking these systems ensures they function optimally.
3. Variable Pressure Zones
Challenge: Different stages of dyeing and finishing might require varying pressure levels. Managing these changes without causing system overloads can be challenging.
Solution: Implementing pressure regulation and monitoring devices within the piping system allows for smooth transitions between different pressure zones. Safety valves can be installed to release excess pressure and prevent system damage.
4. Scale and Deposit Formation
Challenge: Over time, residues from chemicals and hard water can form scales and deposits inside pipes, reducing efficiency and potentially causing blockages.
Solution: Regular cleaning and maintenance, combined with the use of water softeners or descaling agents, can mitigate this issue. Periodic inspections using tools like ultrasonic flow meters can detect buildups early, allowing for timely intervention.
5. Environmental and Safety Concerns
Challenge: Handling and transporting chemicals bring about concerns regarding environmental spills and worker safety.
Solution: Incorporating spill containment measures, leak detection systems, and automated shut-off valves can prevent large-scale environmental incidents. Training personnel in handling procedures and emergency responses ensures that minor issues are addressed promptly and safely.
6. System Integration and Automation
Challenge: As textile operations become more advanced, integrating process piping with automation systems and other machinery becomes crucial but challenging.
Solution: Collaborating with technology providers to design integrated solutions, ensuring software and hardware compatibility, allows for seamless operations. Regular updates and system checks ensure that all components communicate effectively.
While challenges in process piping for textile dyeing and finishing are inevitable, proactive measures, technological advancements, and best practices can effectively counteract these issues. Adopting a proactive approach not only ensures the longevity of the piping system but also guarantees the consistent quality of the finished textiles.
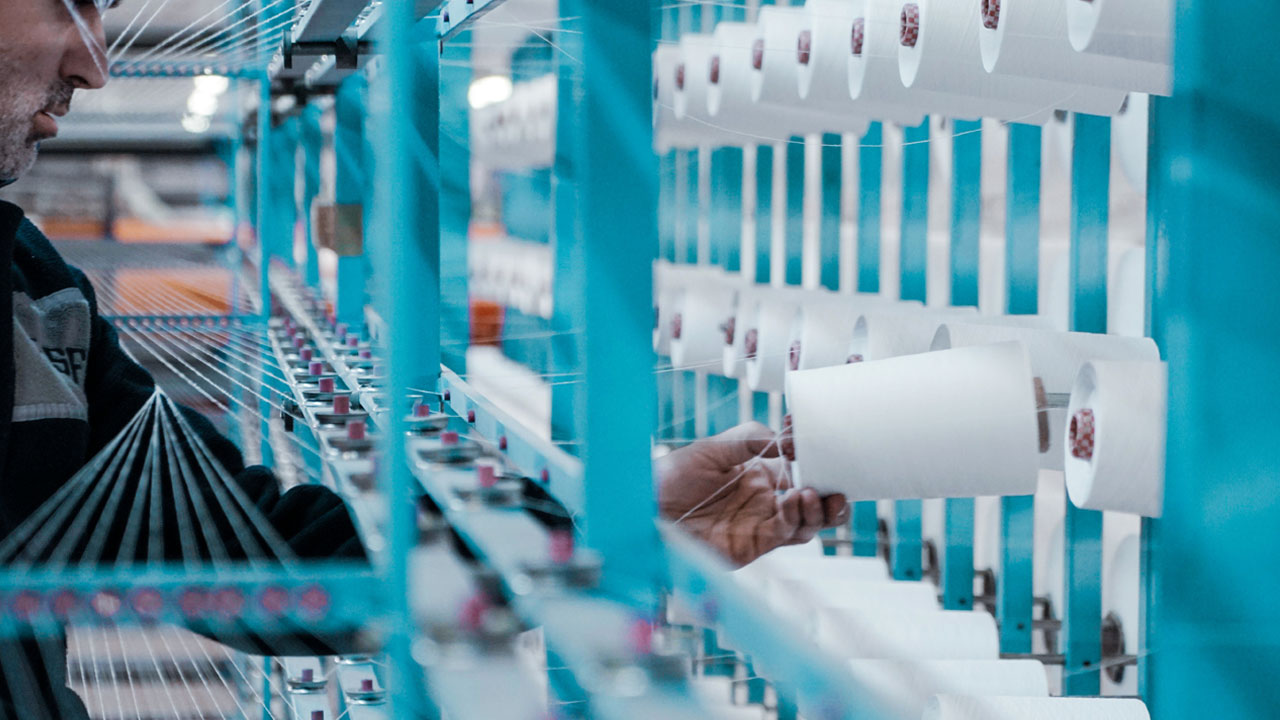
Conclusion
The intricate world of textile dyeing and finishing is a dance of colors, textures, and finishes, all harmoniously coming together to produce fabrics that touch every facet of our lives. Central to this production choreography, ensuring precision and perfection, is the role of process piping. It’s the silent backbone, consistently delivering chemicals, dyes, and treatments at precise timings, temperatures, and quantities.
The importance of process piping transcends its functional role. It directly impacts the quality of textiles, ensuring every hue is vibrant and every finish is flawless. Its efficiency accelerates production timelines, meeting the demands of an ever-evolving fashion world. Moreover, in an age where sustainability is not just a buzzword but a necessity, process piping stands at the forefront, championing water conservation, waste reduction, and energy efficiency.
To textile manufacturers stepping into the future: the path to excellence, innovation, and sustainability is intertwined with the quality of infrastructure you invest in. Process piping systems, with their undeniable significance, deserve keen attention. Investing in state-of-the-art piping solutions is not just a technical upgrade; it’s a commitment to quality, a nod to efficiency, and a step towards a sustainable future.
So, as we pull back the curtains on the vibrant world of textiles, let’s not forget the unsung heroes like process piping that play their part backstage, ensuring the show goes on seamlessly.
Southeastern Process Piping Experts
At Midsouth Mechanical, our commitment to excellence runs deep. We understand the intricate ballet of textile dyeing and finishing and recognize the pivotal role that process piping plays in that narrative. With years of experience and expertise, we are poised to be your trusted partner in ensuring your textile production is top-notch.
Do you have questions about how the right process piping systems can elevate your textile operations? Are you keen on exploring innovative solutions tailored to your unique needs? Or perhaps you simply want a consultation to understand the potential upgrades your infrastructure could benefit from?
Whatever your needs, the team at Midsouth Mechanical is here to assist. Dive into a partnership that prioritizes quality, efficiency, and sustainability. Reach out to us today and let’s chart a path to textile excellence together. Your vision, powered by our expertise, is a recipe for unparalleled success.
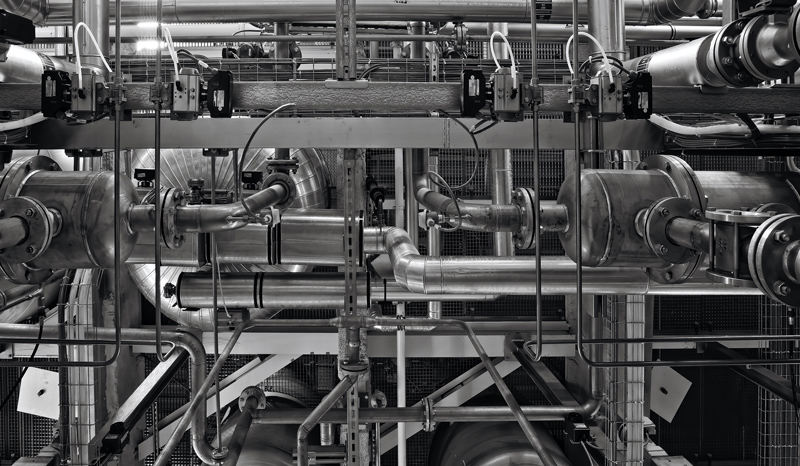
Our team is here to help.
Contact a project manager today!